
Introducing : The Sinterstar Mini
The Sinterstar Mini is designed with Universities, Laboratories, R&D departments and Small to Medium-sized Enterprises in mind:
- Easy and quick to operate, ready for operation within 45 minutes with unseen fast change-over times enable quickly running different processes, tests and products.
- A wide variation of products, including Die-to-Substrate, Die-to-Leadframe, Clips, Preforms and Package-to-Heatsink attach applications, can be sintered with dimensions ranging from 2x2x 0.01mm up to 100x100x80mm.
- The system is equipped with the same intuitive User Interface and application software as with the larger Sinterstar models, delivering maximum process monitoring and control, extended with a fully programmable temperature profile.
- Combines critical high-volume production capabilities such as our patented Silicone-free Dynamic Insert and N2 technologies in an affordable and compact design with 2 installation options:
- The Sinter press can be mounted on top of the Controls cabinet or
- The Sinter press can be placed on a table with the control cabinet next or behind the Tabletop press.
Main Specifications:
- Effective sinter area: 100x100mm;
- Product thickness range: 0,01-80 mm;
- Sinter temperature up to 320⁰C;
- Insert force range: 25N – 196kN;
- Programmable sinter pressure, time and temperature
- Universal Base Tool set for one Dynamic Insert;
- Color touchscreen / HMI;
- Advanced and precise process control with data export functionality;
- Micro Controlled Environment (N2);
- Vacuum Controlled Environment (optional);
- Easy product loading by means of drawer at the frontside;
- Bottom heater/cooler plate is temperature controlled and programmable. Allows heating and cooling of product with adjustable ramp under N2;
Universal Base Tool
This universal Base tool offers great flexibility and is perfect for Research and Quick prototyping purposes. For a unique product only dedicated inserts and alignment plates are required. These parts are easy and fast exchangeable.
The Universal Base Tool consists of:
- Base top tool for 1 Dynamic Insert in a slide
- Base bottom tool including product jig with N2 supply
- Product height conversion set from 0,01-80 mm
- 1x film roll, 50um thickness, 120 mm width, 100m length
3 standard Dynamic insert Units are separately available: 22x22mm, 66x66mm and 100x100mm. Golden samples for pressure uniformity test are included.

Universal Base Top Tool, with 3 Dynamic Insert Units
Dynamic Insert Technology
Our patented Dynamic Insert Technology provides maximum control and guarantees a uniform pressure at every single die or group of dies. The pressure can be varied easily via parameter setting on HMI. Each individual die or each group of die is exactly pressure-, time- and temperature-controlled. Pressure is only applied on the needed areas, resulting in high product density sintering tools and lowest Cost of Ownership.
Micro Controlled Environment
In the Micro Controlled Environment, a single sheet of PTFE film is vacuumed on the loading jig to create within the shortest times a controlled O2 environment by flushing N2. An O2 level below < 50 PPM can be reached. Ideally for sintering Cu area products. I.e. lead frames, Cu-substrates (DBC and AMB), The controlled environment is active during the full cycle; pre-heating, sintering and cooling


Facility Specifications:


Video:
For more information contact your local representative as listed in the Contact section or send an email to: info@boschman.nl
Boschman (NL)
Advanced packaging technology
Stenograaf 3, 6921 EX Duiven
The Netherlands
T +31 26 319 4900
Boschman (SG)
Advanced packaging technology
No. 3 Kaki Bukit Crescent, #01-01, Singapore 416237
T +65 6743 7188
Boschman (CN)
Advanced packaging technology
No. 188, Zixu Road, Xukou Town, Wuzhong District, Suzhou City, Jiangsu Province, China
中國江苏省苏州市吴中区胥口镇子胥路188号
T +86 188 0918 5028
Contact
E info@boschman.nl
W www.boschman.nl
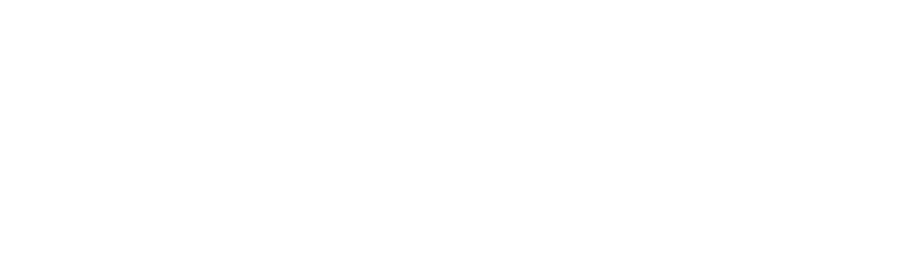